Screen printing (serigraphy) is an ancient printing technique that has played an important role in creating patterns on clothes and packaging, and even on advertising materials, for centuries. Despite the passage of time and the development of modern printing technologies, screen printing is still popular due to its uniqueness and exceptional application. In this article, we will take a closer look at this technique, its history, production process and applications.
History of Screen Printing
The screen printing technique has a long history, originating from ancient stencil printing methods, especially popular in Japan. Initially, paper templates were used, which were applied to a stretched frame of human or animal hair. In Fiji, punched banana leaves were used to make stencils. In the 18th century, screen printing was used to imitate decorative fabrics and wallpapers, and later it was used in the decoration of walls, furniture and other objects. Samuel Simon patented the silk-screen method in Great Britain in 1907, and the technique was developed in the United States during World War I.
Then, the screen printing technique became popular in printing thanks to its versatility. It could be used on various substrates, with various types of paints, including fabrics. In the 1930s, the artistic community experimented with serigraphy, and Carl Zigrosser introduced the term “serigraphy” into the language. The National Association of Serigraphers was founded in the United States, and the first exhibition of prints using this technique took place in 1938.
In the mid-20th century, screen printing gained popularity in Europe and was introduced into the school curriculum. The works of artists such as Andy Warhol or Richard Anuszkiewicz developed this technique within artistic movements such as op-art and pop-art. It is also worth mentioning the use of screen printing in Poland in the 1970s and 1980s, especially in underground printing houses that used this technology to publish independent magazines. Today there is Polish Association of Screen Printing and Digital Printing, which promotes knowledge about printing in Poland.
Screen printing mesh
Traditionally, it was made of silk or cotton threads, but now materials such as nylon, polyester or metal are common. When printing graphics, the most commonly used meshes contain 100 to 150 fibers per square centimeter. This means that the mesh holes have a diameter of 40 to 34 micrometers.
Screen Printing Process
The modern screen printing technique is much more complex than its ancient roots, but the basic process remains the same. Here is a general description of the entire process.
Matrix Preparation
First, a matrix is created. It is a frame made of metal, wood or plastic. A mesh is stretched over the frame and covered with a special light-sensitive emulsion, on which a film with a printing pattern is placed. After exposing this matrix, the black elements on the film are washed out with water, which serve as a pattern for printing.
Printing
The matrix is placed on the material on which the pattern is to be printed. Paint is applied to it and, under the influence of pressure and rubbing with a so-called squeegee, it is transferred to the material through holes in the screen printing mesh. With a multi-color pattern, a matrix must be made for each color separately and this process is repeated over the entire surface for each color, creating the final pattern.
Drying
After printing, the material must be properly dried for the print to become permanent. Depending on your needs, you can use various drying methods, such as hot air or infrared lamps.
Gallery of the screen printing process
Applications of Screen Printing
Screen printing has a wide range of applications in many fields. Below are some examples.
Textiles
Screen printing is often used for printing on fabrics, which allows you to create unique patterns on clothes, towels, tablecloths and other textiles.
Advertising and Posters
Screen printing is a popular technique for printing advertising posters and other promotional materials.
Packaging
Many manufacturers use this technique to add attractive patterns and information to product packaging.
Art and Decorations
Screen printing technology can be found in galleries and on applied arts such as art posters, tablecloths and pillow covers, and the like.
Contemporary Innovations
Although the traditional screen printing process remains the same, the technology and materials used in this field are constantly evolving. Modern screen printing can be performed on various types of surfaces, including glass, metal and plastic. Moreover, modern screen printing machines are much more precise and effective, and the paints used are very resistant to weather conditions and retain their colors for a long time.
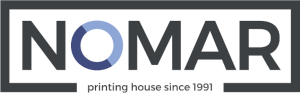
Are you interested in working with us?
Go to the contact tab or
Summary
Screen printing is a printing technique that has deep historical roots, but is still widely used in many areas of modern life. Its uniqueness lies in the ability to print on various materials and create durable patterns. Although many other printing techniques have been developed, screen printing still remains an irreplaceable tool in decorating textiles, advertising and many other products.
FAQ
Can screen printing be used on round surfaces?
This technique can be used on surfaces other than flat ones, e.g. bottles or cups.
Can a multi-color pattern be applied with screen printing?
Yes you can. Each part of the pattern in a given color must be exposed to a separate printing mesh and each color must be applied separately.
When is the best time to use screen printing?
It works best in situations where high durability, color durability and pattern accuracy are required. All types of utility textiles, plastic or paper bags, outdoor advertising and posters.